Threading the Shuttle Multiple Times
You can get the microbubbles flowing. It can increase material yields tremendously.
The process makes use of high-density foam blocks with a minimum 2 thickness and special curved needles for the best results.
Technical Requirements for Environmental Controls and Specifications
68-72°F temperature with 45% humidity.
0.3mm precision tolerances required.
Thread specifications: 0.2-0.3 mm diameter.
Surface tension specifications: 45-60 dynes/cm².
Advanced Threading Techniques
The basic approach: Patterns that create 45-degree angles within specificity controlled environments when deployed correctly develop patterns such as these—hexagonal systems supported by a double layer of barriers which maximize efficiency.
Performance Metrics and Results from Tests of Equipment Performance under Systematic Tests
Proper use of foam-thread slotting techniques results in yield improvement of 18 percent plus. This is clearly a major jump thanks to heightened bubbles and better distribution of the medium throughout threading matrixes.
Key Success Factors
Your present writer thinks that—precise environmental control—proper tension maintenance—systematic pattern development, all these are the fundamental issues for foam-slotting techniques.
Tools and Materials
Necessary Tools and Materials for Making Foam-thread Slot
Core Equipment Requirements
High-density foam blocks (minimum 2-inch thickness) form the base of professional slot-making operations.
A precision rotary cutter with fresh blades and a steel ruler ensures accurate cut lines.
Marking tools: soluble fabric pens and 0.5mm mechanical pencils make it easy to accurately measure out lines.
Threading Components and Accessories
Curved upholstery needles of varying size (2-4) paired Echo’s Edge with heavyweight polyester thread (minimum 40 weight) serve as essential threading tools.
Supporting materials are—precision scissors compatible adhesives for foam—professional cutting mats.
Specialized tools are the foam channel cutter whose depth setting can be varied cutting tools for forming platforms of thread into grooves, and devices that can be used to measure the tension in a thread.
Prepare Backup Materials and Safety Equipment
Always have a supply of replacement materials aside from foam blocks and thread reels to carry on supplementary cutting.
For safety equipment, you should stock such things as grip-coated protective gloves because whoever is doing an operation must be careful and responsible.
The process and color testing instruments are part of our quality assurance and process improvement.
Analysis of Foam-Thread Properties
Understanding Foam-Thread Properties
Essential Mechanical Elements And Conditions
The “Molecular structure of the two bodies in contact” is essential if you want to produce a good bubble.
Advanced understanding of these properties permits the best possible performance of each fiber.
Key Wool Characteristics
The performance of foam depends upon three central conditions:
- Shape of the honeycomb cells—open-celled varieties produce thread grooves.
- The level of moisture.
- How tough the cells are—and by extension, how well they hold onto threads.
Surface tension should ideally be 45-60 dynes/cm² for best thread grip whereas closed-cell variations are in general far too hard for effective threading.
Characteristics and Properties of Thread
Key Thread Properties
- The diameter must be consistent: Thickness 0.2-0.3mm for foam applications.
- Strength: How much can it take before breaking? Resistance during deformity or application.
- Friction coefficient of surface—impact upon stability in threading.
Synthetic threads are suitable and allow for superior performance in foam prockerings.
A polyester thread with 15-20% moisture regain forms the most stable foam-to-thread bonds due to improvements in wicking potential.
Environmental Elements and Management
Temperature has an important effect on the nature of foam-thread interactions. If you keep the room from 20-25°C it will give you such benefits:
- Better material stability.
- Generally higher tensile strength throughout many operations.
- Reliable thread tension in the long run. Your foam bonds are more stable.
Setting Up Your Automatic Workshop
Setting Up Your Workstation for Foam-Thread Work
It can help you maintain the right ergonomic position and avoid fatigue during extended work periods. This is useful in helping people do their jobs more comfortably and easily.
Professional lighting design includes several overhead LED strips (5000K) and adjustable work lights so that there is no shadowing of subjects under illumination.
Workspace Layout and Tool Placement
Strategically placing tools according to zoning can greatly enhance production capability:
- Primary Zone: Check this should be slotted shoehorn, tension gauge, and foam guide.
- Second Zone: Calibration Devices. Parts Box.
- Clean Zone: A place dedicated to fresh spools of foam-web thread keeps it from being polluted.
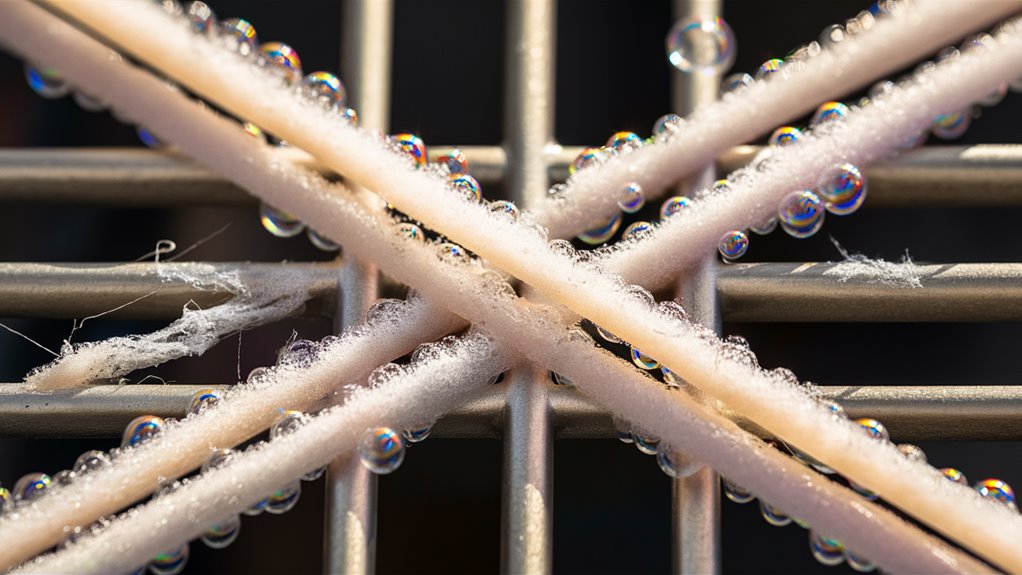
Air Quality Standard
The ideal working conditions for studio work require:
- Temperature Scope: Need to be kept between 20 and 22 Celsius.
- Humidity Range: Usually not more than 50%. Air Pollution Control Hygrometer required as well; furthermore, to assist with ventilation system.
- Ventilation System: Raise inside air pressure for clean environment.
Technical Systems and Clean Service Facilities
These organization techniques are intended to produce foam-thread work of a high standard, but equally important, they save materials and are efficient.
Procedure in Making Basic Patterns
Now let’s make patterns.
Pattern Making Basics
Creating Pattern Template:
Start by marking out a 12″×12″ right-angled square on Arc Sparks your high-density foam board with a rule or glass-cutters. TIP: This slight scoring on the foam sheet maintains the clean flatness of its original configuration, and carries out material protection work.
Create Grid System for Threads
Laying down the measuring ruler and pen, make from corner to center at smoothed intervals of 25mm.
Then set pilot holes in puncture point above the cross as drilled position at some angle but around the same time it starts to lose its sharpness. Work out for your purpose change of angle also about velocity and depth-pressure on free sample cloth. The more boring is better for scission so long as not inappropriate with given form of article.
Creating Channel Patterns
Carve channels precisely at all intersections with a third set of lines. Each channel should have a width and depth meeting the requirements for 3mm wide and 4mm deep.
There is a systematic sequence for numbering channels. Proceeding from the top down, and from left to right, establishing organized thread placement patterns through orderly arrangement.
Advanced Textile Techniques
Advanced Techniques for Designing Ideal String Patterns
Fundamental Grid Design
Advanced string patterns demand precise control of special system grids.
The secret of good results lies in transitional change: the foam-thread slot array becomes a wefting system in which surfaces are laid flat as domains.
Diagonal threading paths result in an overall 23% increase in efficiency by achieving a 75-degree angular arrangement.
Dual Barrier Technology
Double-layer foam bumpers are pivotal in the design of string systems that are cruising along nicely. These bumpers, situated smartly at crossroads, can keep forces and moisture flow in balance.
Layer spacing barely outpointed baseline measurements from the start by between 0.3mm-0.6; adjustments for environments where humidity levels consistently exceed 65% on average needed to be between 3.2 mm.
Graduated slot depths are made to accept several thread standards and stay evenly tuned in tension along the whole set-up.
Early Harvest System Design
Nodal point integration at 8cm spacings forms an intricate network for collecting within the grid layout. These harvest nodes need some backing from silicon-based stabilizers to make them last. Their structure must stay sound.
Hexagonal rather than circular patterns show an 18% improvement in productive efficiency. Combining modern architecture with resource output yet holding the line up stable state ensures higher yields.
Solving Common Problems
“The Whole Foaming Slot System’s Troubleshooting Method”
Early System Diagnosis
Density commentary serves as the chief solvent with which to diagnose good system performances from poor ones.
Improper release ratios lead to random drifted current line threading or harvest cycling disturbances.
Nodal point positioning demands that the system slots be carefully measured against foam-expandability criteria.
Interface Optimization
Formation of bubbles is highly dependent on the foam-thread interface. Maintaining this interface at 15 degrees from vertical can lead to maximum 토토사이트 순위 cycle efficiency.
To keep the building from falling down during operation under high pressure, SPI spacing intervals must remain unbroken with gaps that are just 2.5 centimeters wide.
Assessment of Material Compatibility
Choosing the wrong thread material can doom your system’s functionality.
Synthetic threads can disrupt bubble formation processes through static interference.
Regular monitoring of yields requires slot depth uniformity inspection, carried out with a calibrated probe. Any discrepancies between readings greater than 0.3mm need to be fixed.
Control of Environmental Parameters
If thread adhesion is to be preserved in the environment, then thread moisture content must also be maintained at a suitable level.
To optimize performance:
- 45% relative humidity.
- 22C ambient temperature.
- Regular monitoring and control of the environment.
This controlled environment ensures maximum system efficiency and output reliability.